Viking Drill and Tool — Drill Troubleshooting
Drill bits are cutting tools used to create cylindrical holes, almost always of circular cross-section. Drill bits come in many sizes and have many uses. Bits are usually connected to a mechanism, often simply referred to as a drill, which rotates them and provides torque and axial force to create the hole. Broken Drill Bits
Cause:
-
1. Flutes clogged with chips, drill binds in hole (Common in deep holes)
2. Drill binding due to worn outer corners
3. Work insecurely held
4. Excessive feed
5. Improper point
6. Twist drill is dull
Correction:
- Use a drill with wider flutes and/ or faster helix angle
- Consider polished flutes
- Withdraw drill at regular intervals to clear chips
- If chips are not broken up, consider heavier feeds OR a chip breaker design.
- Repoint or replace drill bit
- Check for excessive speed, inadequate or incorrect coolant, excessive run out as drill enters work material
- Use adequate holding or clamping devices
- Reduce feed
- Check for correct lip clearance
- Use proper type of drill and point for the application
- Replace before dulling occurs. Check Feeds, Speeds, and No. 5 for premature dulling
Broken Tang
Cause:
-
1. Shank or Socke damaged
2. Twist Drill not properly seated in socket
Correction:
- Repair OR Replace
- Check for positive, secure fit
Chips Not Breaking Up
Cause:
-
1. Insufficient feed
2. Improper style of drill and/or point
Correction:
- Increase feed
Damaged Point
Cause:
-
1. Using hard object to tap drill into socket
2. Dropping, Mishandling drill bit
Correction:
- Use soft lead, plastic, etc. hammer
- Handle with care
Over-sized Hole
Cause:
-
1. Drill point off center
2. Machine spindle not rigid OR Not running true
3. Work piece loose and/ or vibrating
Correction:
- Repoint accurately OR Replace with properly pointed drill
- Repair if possible; consider use of bushing
- Tighten and hold securely
Rough Hole
Cause:
-
1. Incorrect point grind and/or dull drill
2. Excessive feed
3. Incorrect or Insufficient coolant
Correction:
- Repoint or replace with properly pointed drill
- Reduce feed
- Correct and Adjust
Poor Tool Life
Cause:
-
1. Coolant not reaching drill point or insufficient or incorrect coolant
2. Speed too high and/or feed too low
3. Wrong type of point and/or drill for application
Correction:
- Correct and Adjust
- Review and Adjust
- Review requirements and conditions
Web Splits
Cause:
-
1. Insufficient lip clearance
2. Point thinned too much
3. Excessive feed
Correction:
- Repoint OR Replace with properly pointed drill
- Repoint OR Replace with properly pointed drill
- Reduce feed
Chipped Lips
Cause:
-
1. Excessive lip clearance and/ or heel relief
Correction:
- Repoint or replace with properly pointed drill
Cutting Edge Chipping
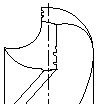
Cause:
-
1. Large run out after attached to machine, loose holder
2. Cutting speeds or feeds is too high
Correction:
• Check holder and/or select another holder• Reduce cutting Speeds OR Feeds
Broken Outer Corners
Cause:
-
1. Insufficient or incorrect coolant
2. Excessive speed
3. Scale, Hard spots encountered in material
Correction:
- Correct and Adjust
- Reduce speed
- No final remedy. If this condition is prevalent; lower feeds and speeds may help